Toward the global market with processing technology and materials
Koide Manufacturing Co.
Cymbals are an indispensable percussion instrument for all kinds of music, from classical, jazz, and rock to brass bands. Koide Manufacturing Co., Ltd. is the only Japanese manufacturer of cymbals. We visited the company of four employees who, through trial and error, established the "Koide Cymbal" brand, which is now attracting worldwide attention.
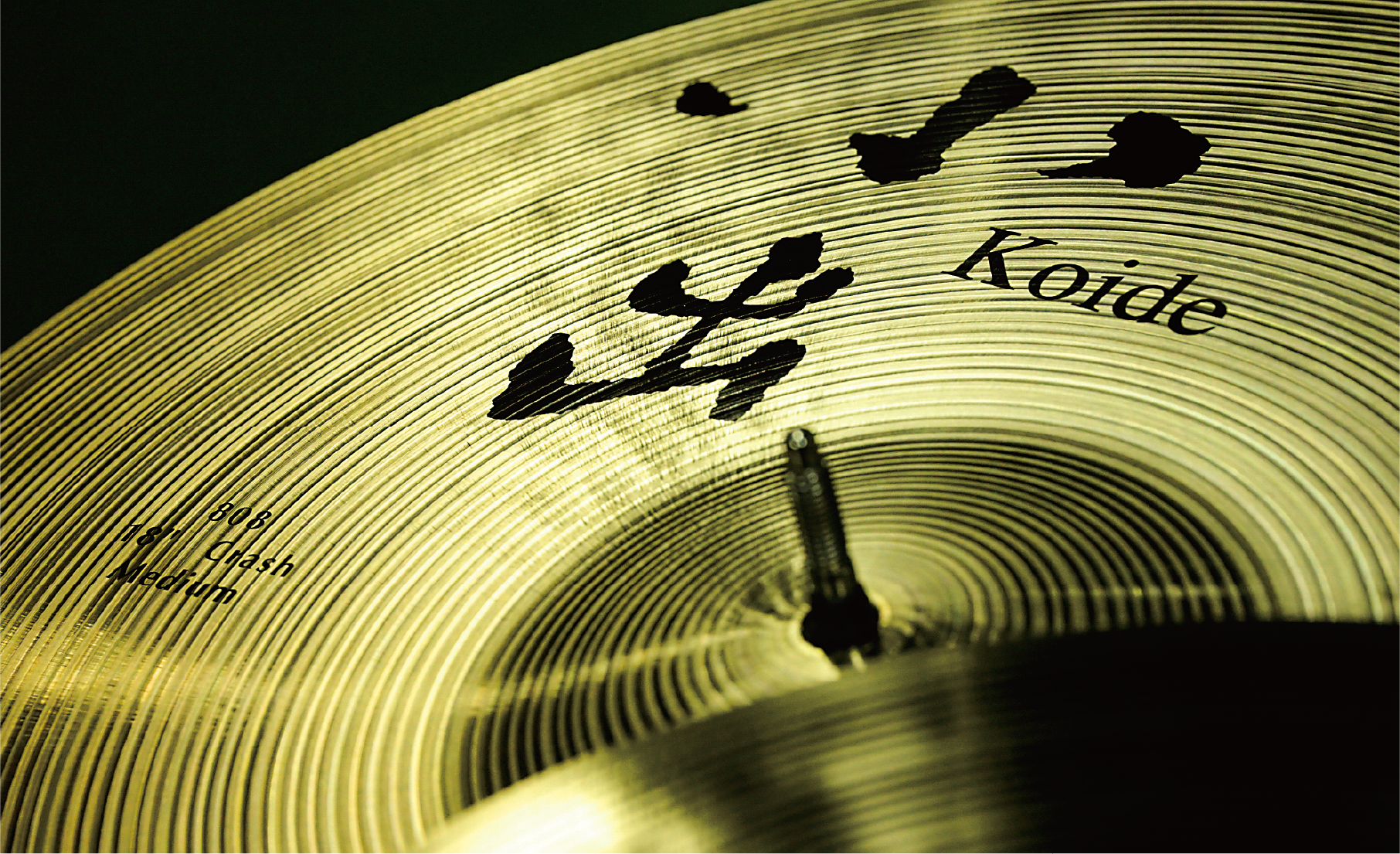
Hammering and lathe processing are the deciding factors.
Cymbals made of bronze are said to have been produced since around 3000 BC. The manufacturing process is unique. High-tin bronze, an alloy of copper and tin, is fired in a furnace and then hot-pressed into a shape with a raised center while it is still soft. The material is then re-hardened several times and shaped by the spatula-drawing process. Then, the thickness and other details are adjusted by hammering and turning.
The shape and material determine the sound. The length of the vibration is adjusted by the number of hammering operations and sharpening. For example, increasing the number of hammers makes the vibration more complex, resulting in a softer sound and a cymbal for jazz.
The way materials are synthesized also makes a difference in sound. Cymbals made by Koide Manufacturing from iron and zirconium-containing materials stop sound quickly and are easy to use as drum cymbals. On the other hand, cymbals made with 23% tin have a sound that rises quickly and lasts for a long time, so they are well known for being easy to use as a matching cymbal, which is played with both hands. We are the only cymbal maker in the world that makes a difference in sound by using different materials. We are able to do this because we collaborate with domestic material manufacturers who can develop such difficult materials," says President Koide.
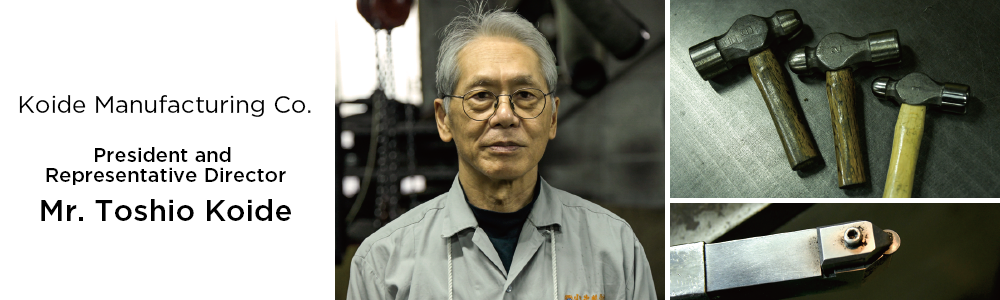
Started researching materials pursue the real thing
Founded in 1947, Koide Seisakusho has been manufacturing parts for commercial washing machines and railroad cars using reliable metalworking techniques such as spatula shaping. The company has also had a long relationship with musical instruments, manufacturing brass cymbals in the 1960s, when group sounds were popular. However, the unit price of brass cymbals was low because they were easy to manufacture, and delivery times were tight, so we discontinued production.
When I told this old story to one of my employees, who played the drums as a hobby, he said, 'Let's make real cymbals. That was about 20 years ago.
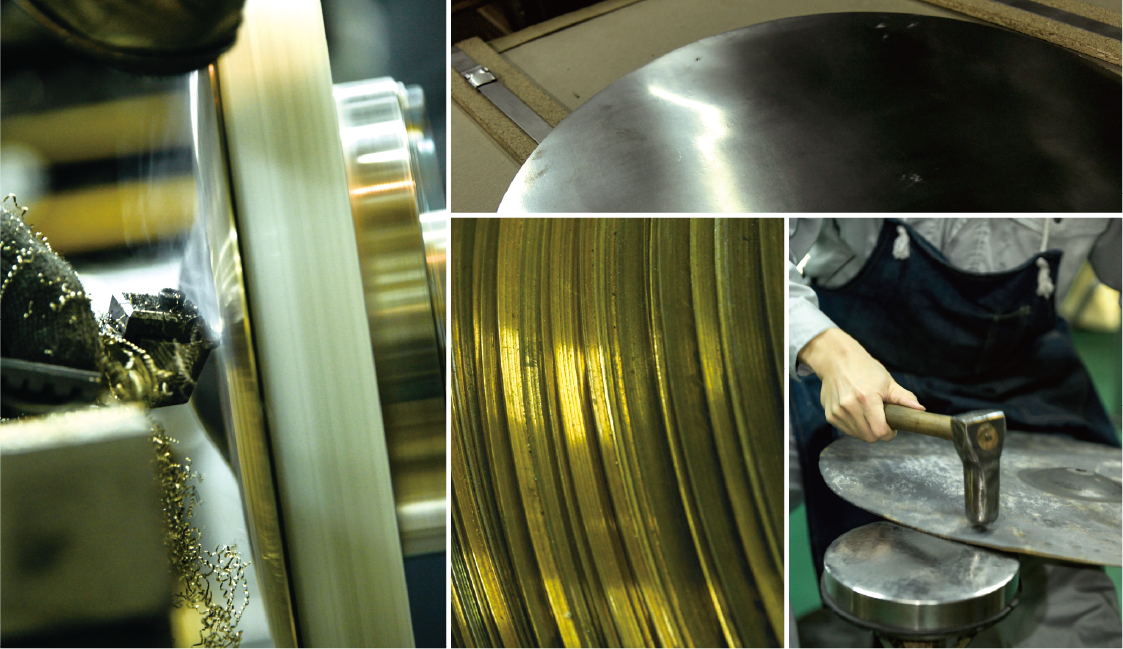
Our first step was to research the material. We found that bronze contained about 20% tin, but there were no domestic manufacturers of high-tin bronze sheets. Hard bronze is not deformable, so it cannot be processed, and there is no other use for it other than cymbals. Since it is resistant to rust, it is used for waterworks and shipbuilding parts, but these parts are basically made by casting," he said. Since then, he has spent three years looking for suppliers and has finally been able to obtain it from overseas manufacturers.
Processing was also an issue. The material is too hard and difficult to handle. There is a considerable deviation from the general feeling of metalworking," said President Koide. Moreover, hammering requires skilled workmanship, and it takes an hour and a half of continuous hammering to produce a single cymbal. The hammering process directly affects the vibration, so we made our own hammering machine that allows us to make cymbals in the same way as if they were struck by hand," says Koide.
The turning process, which transmits vibrations to the cymbal's surface and adjusts its thickness, also requires skill. It's a tricky process, so I made a lot of mistakes at first," he says. Carbide tools are used for the groove cutting edges, and diamond tools are the only tools that can compete with the hard materials covered with an oxide film. Ordinary copper alloys can be machined with HSS tools, but high-tin bronze is impossible.
Thus, overcoming various hardships, "making real cymbals" has grown into a business that accounts for half of our sales. It also led to the development of human resources. A young engineer who was a member of a brass band in high school shared his passion for "making real cymbals" and quit another company to join Koide Manufacturing.
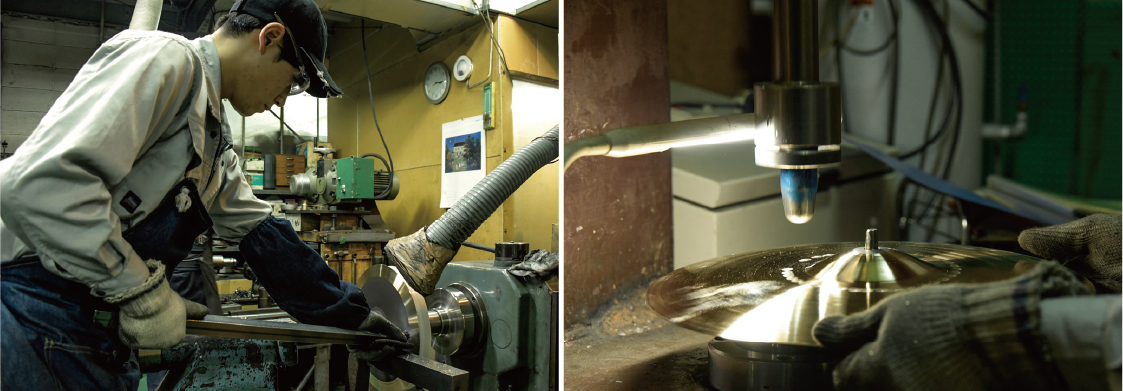
Used by top musicians
Koide Manufacturing's strength lies in the diversity of domestically produced materials. President Koide recalls that it was a fateful encounter with a cooperative material manufacturer. When we were planning to make our own cymbals, a senior executive from the manufacturer called us out of the blue. When I told him about our material problems, he said, 'We'll take care of it. It was thanks to the manufacturer's development and technical capabilities.
Recently, a new material with exquisite addition of titanium has been gaining sales in the field of brass bands. The new material has excellent sound quality with little variation, so it sounds well even if the player has no playing technique, and it fits in with school education, such as brass bands. On the contrary, professional orchestras with good technique don't use it," he says. It seems that the company's ability to respond to needs is becoming more and more brilliant.
While it's being made, it doesn't make a clean sound. We let it sit for a few days after completion and check the sound at the timing when the uneven atoms are in place, but even at that stage we are not sure. But when a good player strikes it, we are amazed at why it sounds so good. Even after completion, it is possible to change the sound produced by the player's technique. Many famous musicians are patronizing Koide cymbals, and they are beginning to attract attention even in the United States, the home of cymbal manufacturing. With the technical and material strengths of Made in Japan, our goal is the global market.
Koide Manufacturing Co.
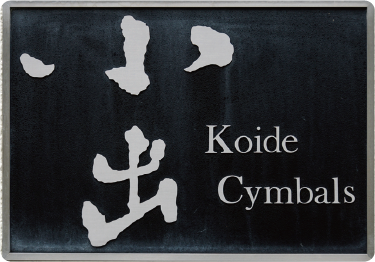
1947
Business:
Manufacture of metal products
Head office:
1-22-32, Shokakuji, Kami, Hirano-ku, Osaka City, Osaka
TEL. 06-6791-1824
http://koidecymbal.com/
This article was published in 2021.